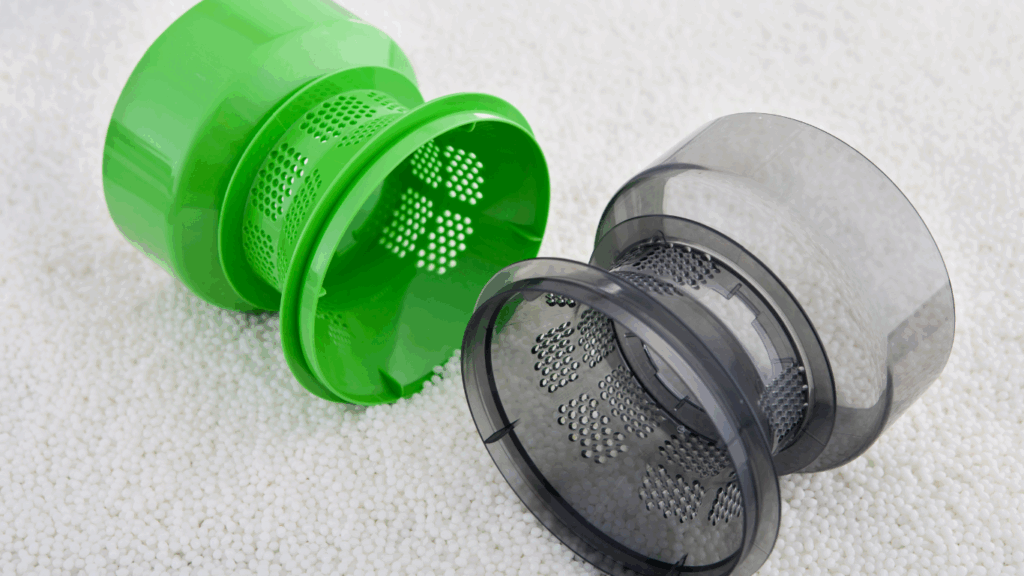
Our services as a plastic injection molding manufacturer
Materials
Thermoplastics and elastomers as single component and mulitcomponent parts
Subsequent processing
Printing, embossing, welding and Pressed-in parts.
Sampling
We carry out all sampling for new project starts in-house and qualify them professionally.
Precision Plastic Injection Molding by Steron Solutions
Plastic injection molding, also known as injection moulding, is a highly efficient process for producing high-quality plastic components. At Steron Solutions, we provide end-to-end injection molding services — from precision tooling to final part production — delivering accurate and cost-effective manufacturing solutions.
Our tailored injection molding tools and precisely molded plastic parts reflect our commitment to quality and precision. While Steron Solutions is a newly established company, our team brings industry know-how and a dedication to delivering reliable, high-performance solutions from day one.
The Injection Molding Process at a Glance
Our injection molding process involves several critical steps:
1. Tool Preparation: The injection mold is first cleaned and installed into the injection molding machine. Key parameters like temperature and pressure are set for optimal performance.
2. Material Melting: Thermoplastic material is melted in a heated barrel, preparing it for injection.
3. Injection Phase: The molten plastic is injected under high pressure into the mold cavity, ensuring complete filling without air pockets.
4. Cooling & Solidification: The plastic cools and solidifies into its final form. This stage is crucial for maintaining product quality and minimizing cycle time.
5. Mold Opening & Part Ejection: The mold opens and the finished part is removed—either manually or automatically.
6. Post-Processing: Parts often undergo additional steps such as sprue removal, trimming, grinding, painting, or surface finishing.
7. Cycle Repeat: The process then repeats for the next production cycle.
Whether using single-component or multi-component injection molding, Steron Solutions is equipped to produce both large-scale production runs and small-batch prototypes with the same precision and efficiency. Our modern injection molding machines ensure a reliable, automated, and high-performance manufacturing process every time.
Types of Plastics: Possible Materials for your plastic molding are:
1. Standard Plastics PE, PS, PP…
2. Engineering Plastics such as ABS, PA6, PET, PBT, PMMA, PC…
3. High-performance plastics such as PEI, PBI, PPS, PPE, LCP…
4. Bio-based plastics
We also offer many materials reinforced or filled. We obtain the granules from well-known suppliers such as Covestro, BASF, Albis, etc.
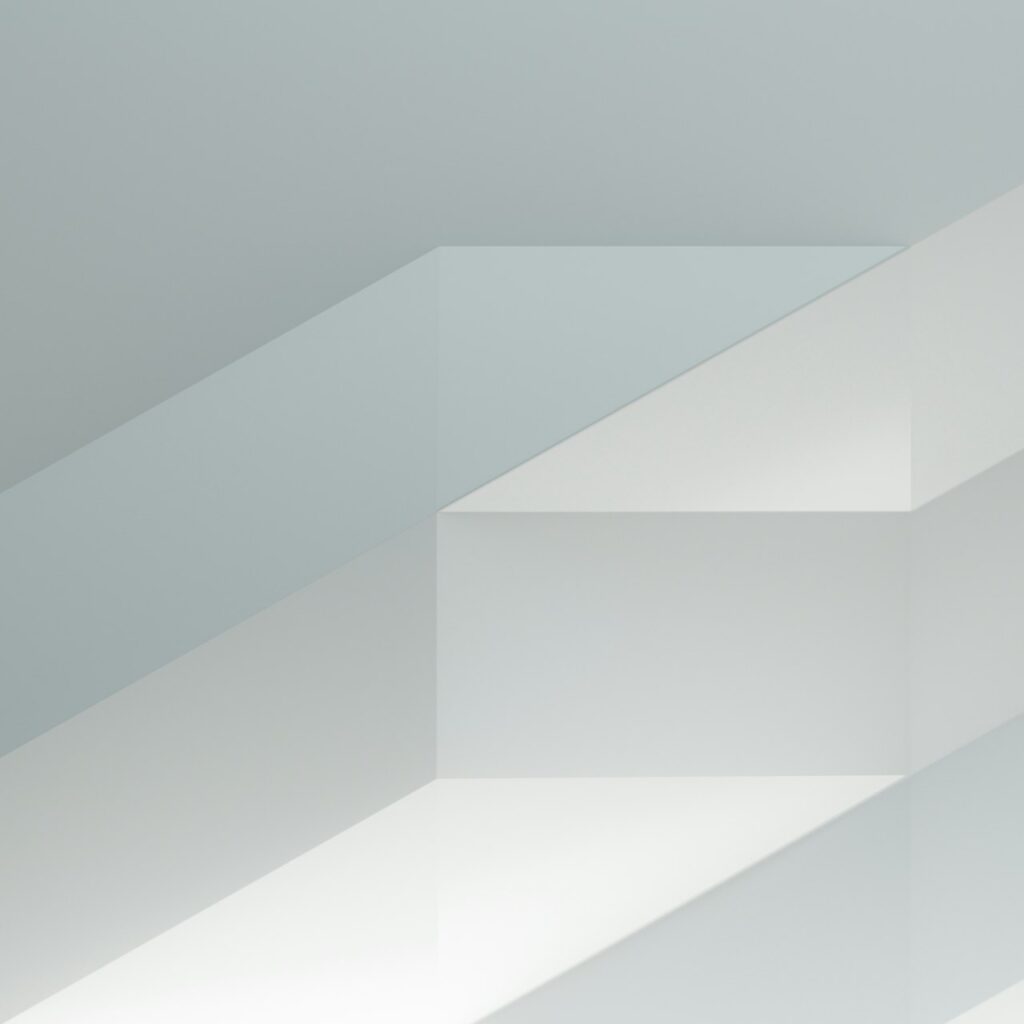
Steron Solutions – Your Full-Service Partner
As a full-service provider, Steron Solutions brings together expertise in injection molding, cable assembly, device assembly, and toolmaking — offering everything you need for plastic part production from one source. You can also choose to use services from individual business units, tailored to your project’s specific needs.
We welcome your inquiries and are ready to work with you to develop a custom injection-molded solution that meets your technical and business requirements. Let us show you why so many clients trust our capabilities.
Contact our injection molding experts today – we look forward to supporting your success.
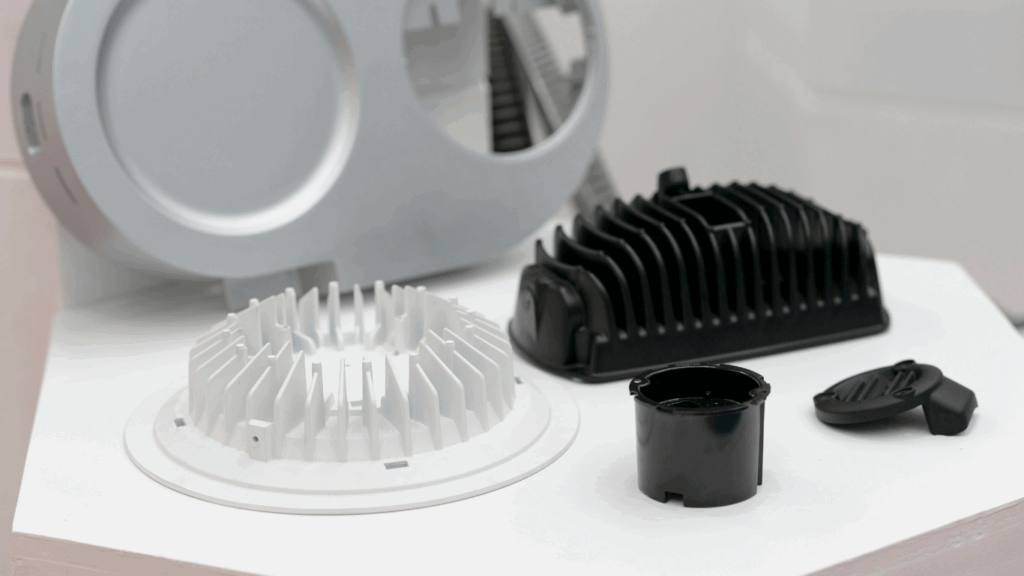
Durable, Functional, and Visually Appealing Surfaces – Tailored to Your Needs
With the right finishes, we specifically increase the durability, resilience, and user-friendliness of your plastic parts. We use a wide range of processes to optimally meet the specific requirements of your application:
1. Scratch- and chemical-resistant coatings, ideal for control elements used in medical devices or industrial automation.
2. Laser marking for high-precision, abrasion-resistant labeling — perfectly suited for buttons, nameplates, or HMI interfaces.
3. IMD (In-Mold Decoration) for integrating decorative and functional surfaces directly during injection molding — perfect for UV-stable, scratch-resistant, and chemical-resistant control panels with high design flexibility, such as in automotive interiors or smart home devices.
4. Off-the-tool surface texturing, where the final surface structure is created directly in the mold — eliminating the need for post-processing and allowing cost-efficient production of high-contrast designs while minimizing visible molding marks like flow lines or weld lines.
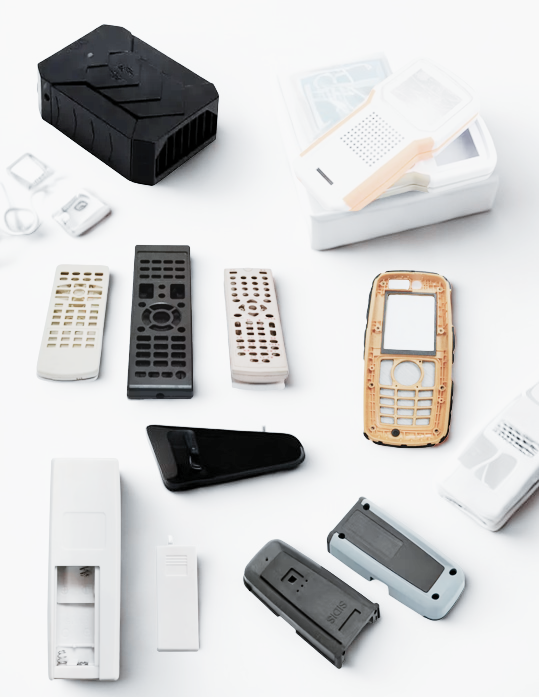
Steron Solutions LLP
Steronsolutions.com
Maharashtra, India
+91 8208123334
info@steronsolutions.in